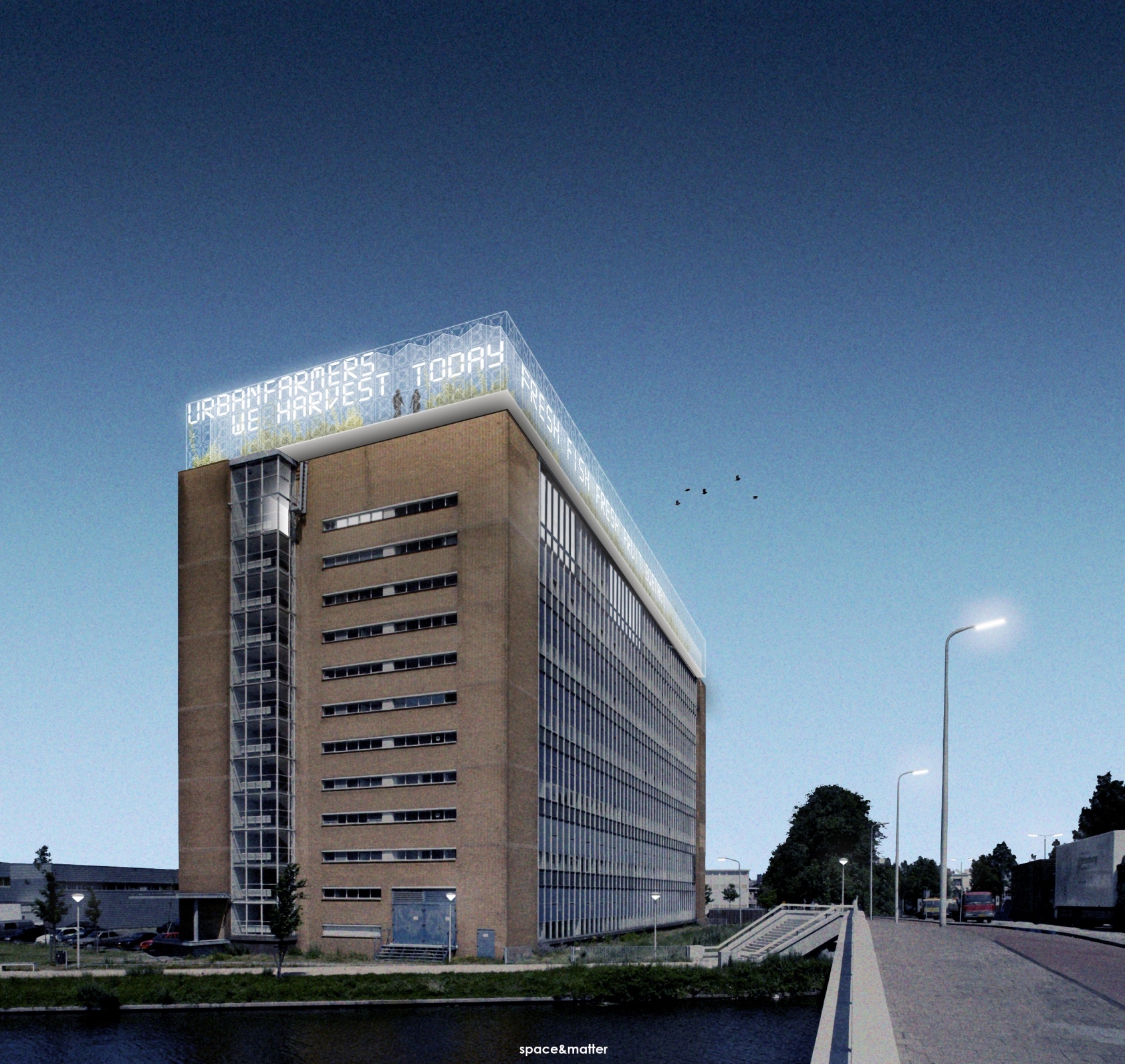
Europe’s biggest commercial urban farm will soon be located in this building in The Hague, in South Holland.
Vegetables will be grown in a 1,200 sqm greenhouse to be placed on the roof of what is known as the De Schelde building, a former Philips factory now partially empty.
Its conversion into a multi-storey urban farming centre – to be called Urban Farming De Schilde – will involve a €2.6 million investment, according to the Municipality of The Hague, which aims to become a climate-neutral city by 2040 and says it is offering an attractive rental price to the urban farming tenants.
Indoor fish farm, boutique brewery
Two of the building’s storeys, each measuring 1,500 sqm, have been earmarked for urban farming. An indoor fish farm and boutique brewery are also included in the redevelopment plans.
City farming pioneer UrbanFarmers (UF) AG, a Swiss company, has been awarded the rooftop space of 1,500 sqm and 700 sqm on the 6th floor.
According to UF, the building has great access and visibility from both the city center as well as the neighboring Westland, “the Dutch horticultural cluster and ‘Silicon Valley’ for plant growing and green innovation.”
“The concept is further supported by a digital billboard wrapped around the rooftop farm communicating live status updates around UF and also other information pertinent to what’s going on inside the greenhouse,” it said.
Koppert Biological Systems also involved
UF said it is focused on building cost effective, sustainable and reliable urban agriculture systems. De Schilde is its fourth after similar projects in Basel, Zurich and Berlin.
Koppert Biological Systems is to share its expertise with UF for the new project. “The cooperation with Urban Farmers will not only focus on natural enemies, beneficial microorganisms and biostimulants, as we, in our role as a horticultural supplier, will also work on the production of insects as fish feed,” said Maren Schoormans, Koppert’s sales manager for the Netherlands.
“We will be able to show society and consumers the opportunities our integrated system offers to everyone who wishes to improve the health, resilience and productivity of crops,” he said.